How to Choose the Right Protective Paint for Your Industrial Structure
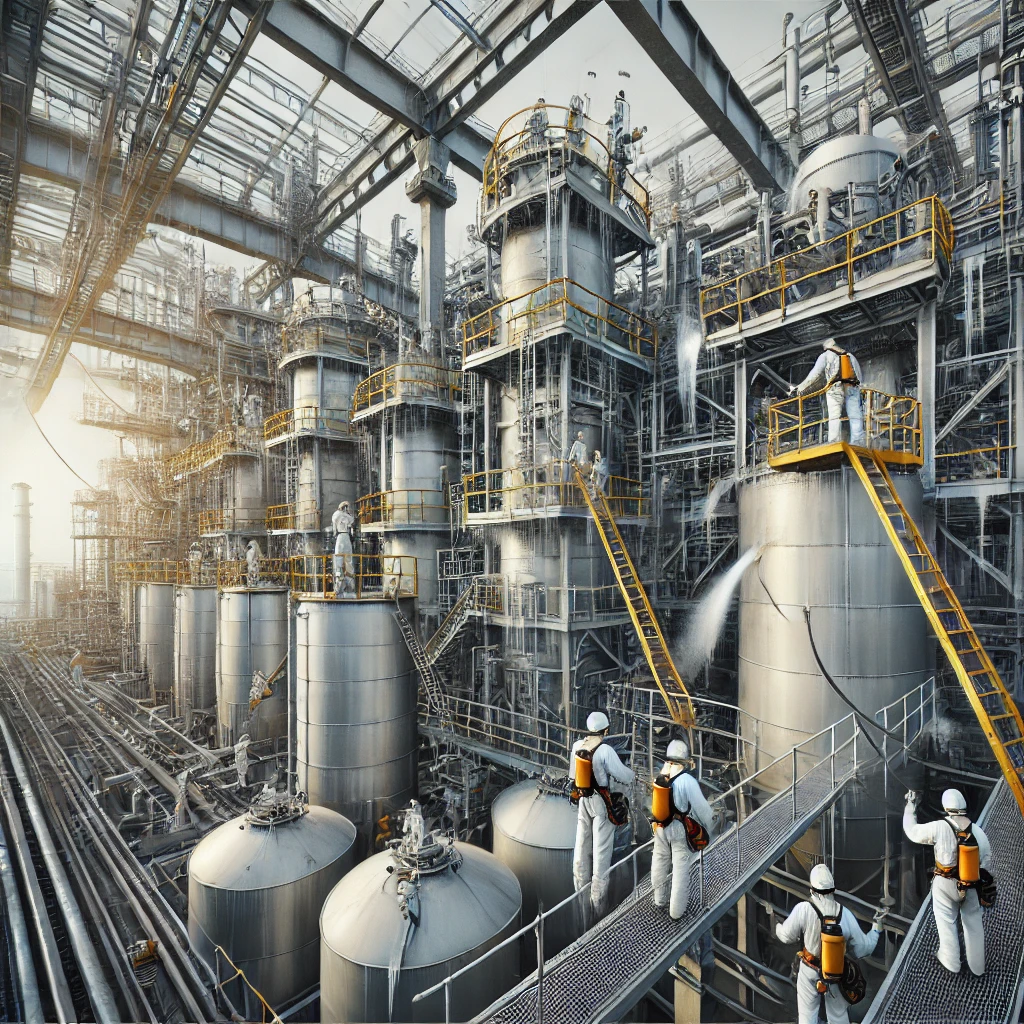
Key Takeaways
- Protective paint is crucial for extending the lifespan of industrial structures by preventing rust, corrosion, and chemical damage.
- Environmental conditions, such as humidity and temperature, significantly impact the choice of protective paint.
- Different surfaces require specific types of paint; for example, metal surfaces benefit from zinc-rich coatings.
- Proper application techniques, including surface preparation and priming, are essential for the effectiveness of the protective paint.
- Regular maintenance, including inspections and minor repairs, ensures the longevity of the protective coating.
Selecting Protective Paint for Industrial Structures
Understanding the Role of Protective Paint
Protective paint serves as a barrier between the industrial structure and the harsh environmental elements it faces. This type of paint is designed to withstand extreme conditions such as high humidity, temperature fluctuations, and exposure to chemicals. Therefore, choosing the right protective paint is critical for maintaining the integrity and longevity of your industrial structures.
For example, consider a factory located near the coast. The salty air can cause metal structures to rust quickly. Using a protective paint that resists salt corrosion can extend the life of these structures significantly.
Essential Factors to Consider
Several factors come into play when selecting protective paint for industrial structures. Ignoring any of these can lead to suboptimal performance and frequent maintenance.
- Environmental conditions
- Surface material
- Longevity and maintenance
- Budget
Key Considerations for Choosing Protective Paint
Assessing Environmental Conditions
The environment where your industrial structure is located plays a significant role in determining the type of protective paint you should use. Harsh weather conditions, such as high humidity, extreme temperatures, and exposure to chemicals, can deteriorate standard paint quickly.
For instance, in areas with high humidity, it is crucial to select a paint that offers excellent moisture resistance. This helps in preventing mold and mildew growth, which can compromise the structural integrity. For more information, check out our guide on weather-resistant paints.
Identifying Surface Material
Different surfaces require different types of protective paint. Metal surfaces, for instance, are prone to rust and corrosion. Therefore, using a zinc-rich coating can offer excellent protection against these issues.
On the other hand, concrete surfaces might benefit more from epoxy coatings, which provide a durable and chemical-resistant finish.
Evaluating Longevity and Maintenance
How long do you want the protective paint to last? Some paints offer longer-lasting protection but may require more complex application processes. It is essential to weigh the benefits of longevity against the effort and cost of application.
Regular maintenance also plays a crucial role. Even the best protective paints require periodic inspections and touch-ups to maintain their effectiveness.
Budget Planning
Budget is always a critical factor. While it might be tempting to go for the cheapest option, remember that lower-cost paints often require more frequent maintenance and may not offer the same level of protection. Therefore, investing in high-quality protective paint can save money in the long run.
Factor | Consideration | Recommended Coating Type |
---|---|---|
Environmental Exposure | Outdoor vs. Indoor | Epoxy or polyurethane for outdoor; Epoxy for indoor |
Chemical Resistance | Type of chemicals present | Chemical-resistant epoxies or vinyl esters |
Temperature Range | Extreme heat or cold | High-temperature resistant coatings for heat; Flexible coatings for cold |
UV Exposure | Sunlight intensity | UV-resistant polyurethane or acrylic coatings |
Moisture Levels | Humidity or water exposure | Moisture-resistant epoxies or polyurethanes |
Abrasion Resistance | High-traffic or impact areas | Epoxy or polyurethane with added aggregates |
Substrate Material | Steel, concrete, aluminium, etc. | Material-specific primers and coatings |
Application Method | Spray, brush, or roller | Fast-drying coatings for spray; Self-levelling for brush/roller |
Regulatory Compliance | VOC restrictions, food safety | Low-VOC or FDA-compliant coatings |
Maintenance Schedule | Frequency of recoating | Long-lasting epoxies or polyurethanes |
Aesthetic Requirements | Colour and finish | Polyurethane or acrylic topcoats for colour retention |
Budget Constraints | Cost vs. performance | Balance between high-performance and economical options |
Types of Protective Paint
Epoxy Coatings
Epoxy coatings are known for their durability and resistance to chemicals. They are ideal for environments where chemical spills are a concern. These coatings adhere well to various surfaces, including metal and concrete.
For example, in a chemical processing plant, epoxy coatings can provide a robust barrier against corrosive substances, ensuring the longevity of the equipment and structures.
Polyurethane Coatings
Polyurethane coatings offer excellent UV resistance, making them suitable for outdoor applications. They are also highly resistant to abrasion, which is ideal for surfaces subjected to heavy wear and tear.
Besides that, these coatings provide a glossy finish, enhancing the aesthetic appeal of the structures they protect.
Alkyd Coatings
Alkyd coatings are oil-based paints known for their durability and ease of application. They are commonly used in industrial settings due to their excellent adhesion properties and ability to withstand moderate environmental conditions. Alkyd coatings are particularly effective on metal surfaces, providing a protective layer against rust and corrosion.
For example, in a warehouse with metal shelving and equipment, alkyd coatings can offer a cost-effective solution to prevent rust while maintaining a professional appearance.
Acrylic Coatings
Acrylic coatings are water-based and offer excellent UV resistance, making them suitable for outdoor applications. They dry quickly and are easy to clean, which is beneficial in environments where hygiene is a priority. Acrylic coatings are also flexible, allowing them to expand and contract with temperature changes without cracking.
Consider a food processing plant where cleanliness and durability are paramount. Acrylic coatings can provide a protective layer that is easy to maintain and resistant to the frequent cleaning chemicals used in such facilities.
Zinc-Rich Coatings
Zinc-rich coatings are primarily used on metal surfaces to provide cathodic protection. These coatings contain a high percentage of zinc, which acts as a sacrificial layer, corroding in place of the underlying metal. This type of paint is highly effective in preventing rust and corrosion, especially in marine and coastal environments.
For instance, offshore oil rigs face constant exposure to salty seawater, which can cause severe corrosion. Zinc-rich coatings are ideal for such settings, offering robust protection and extending the life of the metal structures.
Application Techniques for Protective Paint
Proper Surface Preparation
Before applying any protective paint, the surface must be thoroughly prepared. This step is crucial for ensuring the paint adheres properly and provides the maximum level of protection. Surface preparation typically involves cleaning the surface to remove any dirt, grease, or existing paint, followed by sanding or blasting to create a rough texture that helps the new paint bond effectively.
For example, if you are preparing a metal surface, you might use sandblasting to remove rust and create a textured surface for better paint adhesion.
Priming Processes
Priming is the next critical step after surface preparation. A primer acts as an intermediary layer between the surface and the protective paint, improving adhesion and providing additional protection. The type of primer used will depend on the surface material and the environmental conditions it will face.
For instance, a metal primer containing rust inhibitors can be used on steel structures to prevent corrosion, while a concrete primer can help seal porous surfaces and improve paint adhesion.
Mixing Paint Correctly
Proper mixing of the paint is essential for achieving a consistent and durable finish. Follow the manufacturer’s instructions for mixing ratios and use the appropriate tools to ensure the paint is well-blended. Inadequate mixing can lead to uneven application and reduced protective qualities. For more information on selecting the right paint, visit this comprehensive guide.
For example, when using a two-component epoxy paint, it is crucial to mix the resin and hardener in the correct proportions to achieve the desired chemical resistance and durability.
Application Methods
Several methods can be used to apply protective paint, including brushing, rolling, and spraying. The choice of method depends on the type of paint, the surface area, and the desired finish. Spraying is often preferred for large surfaces as it provides a smooth and even coat, while brushing and rolling are suitable for smaller areas or detailed work.
For example, when painting a large industrial tank, spraying can offer a quick and efficient way to cover the surface evenly, while a brush might be used for touch-ups or hard-to-reach areas.
Applying Multiple Coats
Applying multiple coats of protective paint can enhance its durability and effectiveness. Each coat should be allowed to dry thoroughly before applying the next one, following the manufacturer’s recommended drying times. Multiple coats create a thicker barrier, providing better protection against environmental factors.
For instance, in a high-traffic industrial area, applying three coats of polyurethane paint can offer superior resistance to abrasion and wear compared to a single coat.
Maintaining Protective Coatings
Regular Inspection
Regular inspections are essential for maintaining the effectiveness of protective coatings. Look for signs of wear, such as chipping, peeling, or discoloration, and address any issues promptly. Inspections should be conducted at least once a year, or more frequently in harsh environments.
For example, in a chemical plant, monthly inspections might be necessary to ensure the protective coatings are holding up against constant exposure to corrosive substances.
Minor Repairs and Touch-Ups
Addressing minor damages promptly can prevent them from escalating into more significant issues. Small chips or scratches can be repaired with touch-up paint, while more extensive damage might require reapplication of the protective coating. Keeping a supply of touch-up paint on hand can facilitate quick repairs and extend the life of the coating.
For example, if you notice a small chip in the paint on a metal beam, applying touch-up paint immediately can prevent rust from forming and spreading.
Professional Maintenance Services
While regular inspections and minor repairs can be handled in-house, professional maintenance services offer a more thorough approach. These services can include detailed inspections, surface preparation, and reapplication of protective coatings. Professional services ensure that the protective paint is applied correctly and that any underlying issues are addressed.
For instance, hiring a professional maintenance team for an annual inspection and reapplication of protective paint on an industrial structure can provide peace of mind and ensure the structure remains in optimal condition.
Professional Maintenance Services
While regular inspections and minor repairs can be handled in-house, professional maintenance services offer a more thorough approach. These services can include detailed inspections, surface preparation, and reapplication of protective coatings. Professional services ensure that the protective paint is applied correctly and that any underlying issues are addressed.
For instance, hiring a professional maintenance team for an annual inspection and reapplication of protective paint on an industrial structure can provide peace of mind and ensure the structure remains in optimal condition.
- Detailed inspections to identify potential issues
- Expert surface preparation for optimal paint adhesion
- Reapplication of protective coatings for long-lasting protection
- Addressing underlying issues that may affect the structure’s integrity
By investing in professional maintenance services, you can extend the life of your protective coatings and ensure that your industrial structures remain in top condition. Learn more about enhancing outdoor durability with weather-resistant paints.
Conclusion and Recommendations
Choosing the right protective paint for your industrial structure is a critical decision that impacts the longevity and safety of your assets. By considering environmental conditions, surface material, longevity, maintenance, and budget, you can make an informed choice that meets your specific needs.
Investing in high-quality protective paint and following proper application techniques will provide a robust barrier against harsh environmental elements, reducing the need for frequent maintenance and repairs. For expert guidance on this, consider reading our guide on applying acrylic industrial paints.
Summary of Key Points
To summarise, selecting the right protective paint involves understanding the role of protective paint, considering key factors, choosing the appropriate type of paint, and following proper application techniques. Regular maintenance, including inspections and minor repairs, is essential for ensuring the longevity of the protective coatings.
Protective paint serves as a barrier against environmental elements, preventing rust, corrosion, and chemical damage. Different surfaces require specific types of paint, and proper application techniques are crucial for effectiveness.
Regular maintenance, including inspections and minor repairs, ensures the longevity of the protective coating. Investing in professional maintenance services can provide a more thorough approach to maintaining your industrial structures.
- Protective paint extends the lifespan of industrial structures by preventing rust, corrosion, and chemical damage.
- Environmental conditions, surface material, longevity, maintenance, and budget are key factors to consider.
- Different types of protective paint include epoxy, polyurethane, alkyd, acrylic, and zinc-rich coatings.
- Proper application techniques, such as surface preparation, priming, and applying multiple coats, are essential.
- Regular maintenance, including inspections and minor repairs, ensures the longevity of the protective coatings.
Final Recommendations
When choosing protective paint for your industrial structure, take the time to assess the environmental conditions, identify the surface material, evaluate the desired longevity and maintenance requirements, and plan your budget accordingly. Select the appropriate type of paint based on these factors and follow proper application techniques to ensure the effectiveness of the protective coating.
Regular maintenance, including inspections and minor repairs, is crucial for maintaining the integrity of the protective coatings. Consider investing in professional maintenance services for a more thorough approach to preserving your industrial structures.
IPS Paint Supplies
At IPS Paint Supplies, we provide an extensive range of protective coatings and paints from the industry’s leading brands, including PPG Sigma, Jotun, HMB, and Mipa PMI.
Our products are meticulously designed to deliver superior protection and long-lasting durability for your most valuable assets. Whether you’re protecting industrial equipment, infrastructure, or commercial buildings, our selection of high-performance coatings ensures that your surfaces withstand even the harshest conditions.
Our curated lineup features coatings with exceptional resistance to corrosion, abrasion, chemicals, and environmental factors, making them ideal for diverse applications—from heavy industry and marine environments to architectural and infrastructure projects. With various formulations and finishes available, these coatings not only protect but also enhance the visual appeal of your structures, offering both functionality and aesthetic value.
Choosing IPS Paint Supplies means choosing quality and reliability. We partner with leading brands in the protective coatings industry to bring you products that meet the highest standards of performance and durability. Our experienced team is ready to assist you in selecting the perfect solution for your specific needs, ensuring your investments remain protected for years to come. See details here.
FAQs
To address common questions about protective paint for industrial structures, here are some frequently asked questions and their answers:
Is protective paint suitable for all industrial environments?
Yes, protective paint is designed to withstand various environmental conditions and can be tailored to suit specific industrial environments. However, it is essential to choose the right type of paint based on the specific conditions your structure will face. For more information on selecting the appropriate paint, you can refer to this guide on how to select the right industrial paint.
- High humidity: Moisture-resistant paint
- Extreme temperatures: Temperature-resistant paint
- Chemical exposure: Chemical-resistant paint
- Outdoor use: UV-resistant paint
By selecting the appropriate type of protective paint, you can ensure optimal performance in any industrial environment. For more information, visit Coating Systems.
How often should protective paint be reapplied?
The frequency of reapplication depends on the type of paint used, the environmental conditions, and the level of wear and tear the structure experiences. Generally, protective paint should be inspected annually, and touch-ups or reapplication should be done as needed. In harsh environments, more frequent inspections and reapplications may be necessary.
What are the most cost-effective types of protective paint?
The cost-effectiveness of protective paint depends on the specific needs of your industrial structure. While some paints may have a higher initial cost, their durability and longevity can make them more cost-effective in the long run. For example, epoxy coatings offer excellent chemical resistance and durability, making them a cost-effective choice for chemical processing plants.
Are certain types of paint better for specific materials?
Yes, different types of protective paint are designed to work best on specific materials. For example:
- Metal surfaces: Zinc-rich coatings for rust and corrosion protection
- Concrete surfaces: Epoxy coatings for durability and chemical resistance
- Outdoor structures: Polyurethane coatings for UV resistance and abrasion protection
- Indoor environments: Acrylic coatings for quick drying and easy maintenance
Choosing the right type of paint for the material of your industrial structure ensures optimal protection and longevity.