Modern Industrial Structures Protective Coating Technologies & Solutions
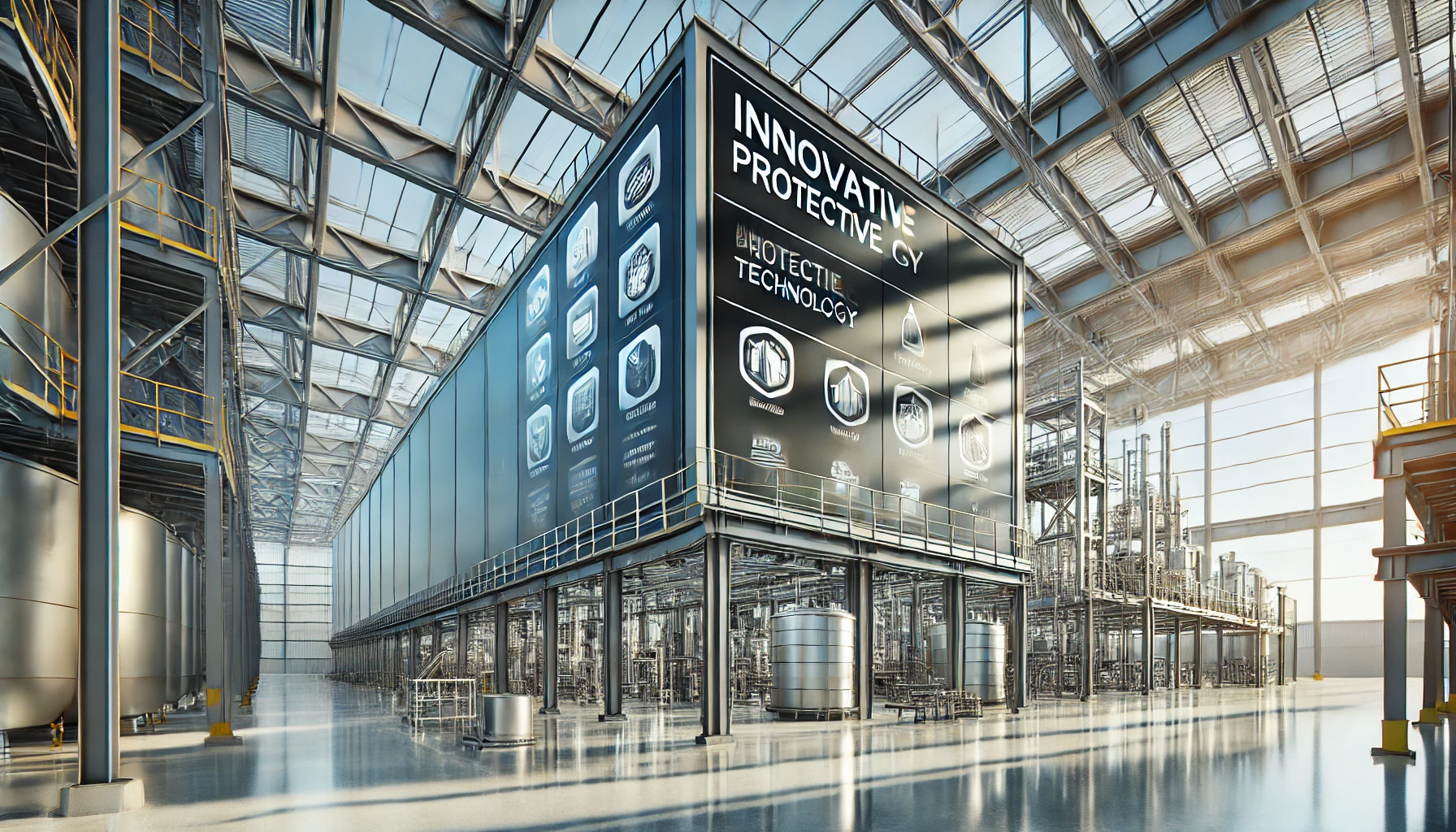
Key Takeaways
- Protective coatings are essential for enhancing the durability and safety of industrial structures.
- Different industries, such as construction and manufacturing, rely heavily on these coatings in the UK.
- Ceramic coatings offer high resistance to heat and corrosion, making them ideal for extreme environments.
- Polymer coatings provide versatility and are used in various applications, including waterproofing and abrasion resistance.
- Intumescent coatings are crucial for fire protection, expanding under heat to form a protective char layer.
Introduction to Protective Coatings for Industrial Structures
Imagine a world where bridges rust away in a few years, pipelines leak hazardous materials, and buildings crumble under environmental stress. This is the world without protective coatings. These coatings are the unsung heroes of the industrial world, ensuring that our infrastructure stands the test of time and the elements.
In the UK, the need for protective coatings is particularly acute due to the variable climate and industrial demands. These coatings play a critical role in safeguarding structures against environmental damage, wear and tear, and even fire. By applying the right protective coating, industries can significantly extend the lifespan of their structures, reduce maintenance costs, and enhance safety.
Purpose and Benefits of Protective Coatings
The primary purpose of protective coatings is to shield industrial structures from damage. Whether it’s corrosion from moisture, abrasion from physical contact, or degradation from chemical exposure, coatings provide a robust barrier. They are like armor for structures, offering a first line of defence against various threats.
Besides protection, these coatings also offer benefits like aesthetic enhancement, thermal insulation, and even energy savings. For example, reflective coatings can reduce heat absorption, lowering cooling costs in buildings. Moreover, certain coatings can prevent bacterial growth, making them ideal for hygienic environments like food processing plants.
Purpose | Benefits |
---|---|
Corrosion Protection | – Prevents rust and degradation – Extends lifespan of metal structures – Reduces maintenance costs |
Chemical Resistance | – Protects against harsh chemicals – Prevents material breakdown – Enhances safety in industrial settings |
Wear Resistance | – Reduces abrasion and erosion – Extends equipment life – Minimizes need for replacements |
Weather Protection | – Guards against UV damage – Prevents moisture ingress – Resists temperature fluctuations |
Aesthetic Enhancement | – Improves visual appeal – Allows for customization – Maintains appearance over time |
Safety Improvement | – Provides slip resistance – Enhances visibility through color coding – Reduces risk of electrical hazards |
Environmental Protection | – Reduces VOC emissions with low-VOC options – Prevents leaching of harmful substances – Contributes to sustainable practices |
Performance Enhancement | – Improves equipment efficiency – Reduces friction in moving parts – Enhances thermal properties |
Hygiene Maintenance | – Offers antimicrobial properties – Facilitates easy cleaning – Prevents growth of mold and mildew |
Cost Reduction | – Decreases frequency of repairs – Lowers long-term maintenance expenses – Extends asset lifetime value |
Key Industries in the UK Relying on Coatings
Several industries in the UK depend heavily on protective coatings. The construction sector, for instance, uses coatings to protect buildings and infrastructure from weathering and decay. This is especially important in coastal areas where saltwater can accelerate corrosion. To explore more about the latest advancements in this field, check out the top trends in industrial architectural coatings.
The automotive industry also relies on coatings for both protective and aesthetic purposes. Coatings help vehicles withstand harsh environmental conditions while maintaining their visual appeal. Similarly, the oil and gas industry uses specialized coatings to protect pipelines and equipment from corrosive substances.
Types of Protective Coating Technologies
Now, let’s delve into the different types of protective coating technologies available today. Each type has unique properties and applications, making them suitable for specific industrial needs.
Among the many options, ceramic coatings, polymer coatings, and intumescent coatings stand out for their effectiveness and versatility. Understanding these technologies can help industries make informed decisions about the best solutions for their needs.
“Ceramic coatings are known for their exceptional heat and corrosion resistance, making them ideal for high-temperature environments.”
We’ll explore each of these technologies in detail, starting with ceramic coatings.
Ceramic Coatings and Their Uses
Ceramic coatings are renowned for their ability to withstand extreme temperatures and resist corrosion. These coatings are made from inorganic materials, typically oxides, carbides, or nitrides, which provide a hard and durable finish.
One common application of ceramic coatings is in the aerospace industry, where they protect engine components from high heat and wear. They are also used in the automotive industry, particularly for exhaust systems and engine parts, to enhance performance and longevity.
Methods of Application
Applying protective coatings requires precision and expertise to ensure optimal performance. The method of application can vary depending on the type of coating and the surface being treated. Common methods include spraying, brushing, and dipping.
Spraying is often used for large surfaces and provides an even coat with minimal waste. It’s particularly effective for complex shapes where brushes might miss spots. Brushing, on the other hand, is ideal for smaller areas or when precision is required. Dipping involves immersing the object in a coating solution, ensuring complete coverage, which is useful for small, intricate parts.
Common Installation Challenges and Solutions
- Surface Preparation: Ensuring the surface is clean and free of contaminants is crucial for adhesion.
- Environmental Conditions: Temperature and humidity can affect the curing process, so it’s important to control these factors.
- Coating Thickness: Applying the right thickness is essential to ensure durability without wastage.
One of the most common challenges is inadequate surface preparation. This can lead to poor adhesion and premature failure of the coating. To overcome this, thorough cleaning and sometimes abrasive blasting are recommended to create a suitable surface profile.
Environmental conditions can also pose challenges during application. High humidity or low temperatures can slow down the curing process, leading to defects. It’s crucial to monitor and adjust the environment as needed or use coatings designed to cure under specific conditions.
Another issue is achieving the correct coating thickness. Too thin, and the coating may not provide adequate protection; too thick, and it can lead to cracking or other issues. Using precise measurement tools and following manufacturer guidelines can help ensure the right thickness is achieved.
Innovations in Coating Technologies
The field of protective coatings is continually evolving, with new technologies and innovations enhancing performance and sustainability. These advancements not only improve the protective qualities of coatings but also address environmental concerns.
One major area of innovation is the development of eco-friendly coatings. These coatings aim to reduce or eliminate volatile organic compounds (VOCs), which are harmful to the environment and human health. By using water-based formulations or novel resins, manufacturers are creating coatings that are both effective and environmentally responsible.
Another exciting development is the use of nanotechnology in coatings. Nanoparticles can enhance the properties of coatings, such as scratch resistance, UV protection, and even self-cleaning abilities. These coatings offer significant benefits in terms of durability and maintenance, making them highly attractive for various industries. For those interested in sustainable advancements, there are eco-friendly industrial coatings that also incorporate these innovative technologies.
Advancements in Eco-Friendly Coatings
- Water-Based Coatings: Reduce VOC emissions and are safer for the environment.
- Bio-Based Resins: Derived from renewable resources, offering a sustainable alternative.
- Low-VOC Formulations: Minimize environmental impact while maintaining performance.
Eco-friendly coatings have become a focal point in the industry due to growing environmental regulations and consumer demand for sustainable solutions. Water-based coatings are leading the charge, offering a reduction in harmful emissions without compromising on quality.
Bio-based resins are another innovative approach, utilizing renewable resources like plant oils to create sustainable coatings. These resins provide a green alternative to traditional petrochemical-based products.
Manufacturers are also developing low-VOC formulations that maintain high performance while reducing environmental impact. These coatings are particularly important for indoor applications where air quality is a concern.
Nanotechnology in Coatings
Nanotechnology is revolutionizing the protective coatings industry by enhancing traditional properties and introducing new functionalities. By incorporating nanoparticles into coatings, manufacturers can achieve superior hardness, increased UV resistance, and even antibacterial properties.
Smart Coatings with Self-Healing Properties
Imagine a coating that can repair itself after damage, much like human skin. Smart coatings with self-healing properties are making this a reality. These coatings contain microcapsules filled with healing agents that release upon damage, sealing cracks and preventing further degradation.
Case Studies of Coating Solutions in the UK
To illustrate the effectiveness of modern protective coatings, let’s examine some real-world applications in the UK. These case studies highlight the diverse applications and benefits of advanced coating technologies.
Infrastructure Projects with Advanced Coatings
In recent years, several infrastructure projects in the UK have utilized advanced coatings to enhance durability and safety. For example, the restoration of the iconic Forth Bridge involved the application of a high-performance anti-corrosion coating, ensuring the structure remains protected against the harsh Scottish climate.
Another notable project is the Thames Barrier, which protects London from tidal surges. The barrier’s gates are coated with a specialized marine-grade coating that resists saltwater corrosion and extends the lifespan of this critical infrastructure.
These projects demonstrate the importance of selecting the right coating technology to meet specific environmental challenges and structural demands.
Successful Industrial Applications
In the industrial sector, coatings are used to protect equipment and machinery from wear and tear. A leading UK manufacturer of wind turbines, for example, uses advanced polymer coatings to protect turbine blades from erosion caused by wind and rain. This not only extends the lifespan of the turbines but also improves their efficiency. Learn more about top-quality coating solutions that can enhance industrial applications.
Lessons Learned and Best Practices
From these case studies, we learn that the key to successful coating applications lies in thorough planning and execution. Proper surface preparation, choosing the right coating for the environment, and adhering to application guidelines are all critical factors.
Importance of Choosing the Right Coating Solutions
Choosing the right protective coating is crucial for ensuring the longevity and performance of industrial structures. The right solution can save money, enhance safety, and provide peace of mind knowing that the structure is well-protected against various environmental and mechanical threats.
When selecting a coating, consider the specific needs of the project, including the environmental conditions, the type of materials being protected, and the desired lifespan of the coating. Each of these factors will influence the choice of coating technology and application method.
To make an informed decision, it’s important to consult with experts in the field who can provide guidance based on the latest technologies and best practices.
Factors Influencing Coating Selection
Several factors should be considered when selecting a protective coating. These include the premier PPG coating solutions available in the market.
- Environmental Conditions: Consider the exposure to elements like UV radiation, moisture, and chemicals.
- Material Compatibility: Ensure the coating is suitable for the substrate material.
- Application Method: Choose a method that suits the project scale and complexity.
- Regulatory Compliance: Ensure the coating meets industry and environmental standards.
For example, a coating designed for a marine environment must resist saltwater corrosion, while a coating for a food processing facility must meet hygiene standards.
“Selecting the right coating involves balancing technical requirements with practical considerations like cost and application feasibility.”
By evaluating these factors, industries can choose coatings that provide optimal protection and value.
Balancing Cost with Longevity and Performance
Cost is always a consideration when selecting a protective coating, but it’s important not to sacrifice quality for price. A cheaper coating might save money upfront but could lead to higher maintenance costs and reduced lifespan.
Investing in a high-quality coating can provide long-term savings by reducing the need for frequent reapplications and repairs. It’s essential to evaluate the total cost of ownership, which includes initial costs, maintenance, and potential downtime.
Conclusion and Future of Protective Coatings
The future of protective coatings is bright, with ongoing advancements in technology and materials. These innovations promise to enhance the durability, functionality, and sustainability of coatings, offering even greater protection for industrial structures.
Trends in Coating Technology and Market Dynamics
Key trends in the coating industry include the development of eco-friendly and smart coatings, as well as the integration of nanotechnology to enhance performance. The market is also seeing a shift towards more sustainable practices, driven by regulatory pressures and consumer demand.
These trends are shaping the future of the industry, with companies investing in research and development to stay competitive and meet the evolving needs of their clients.
Recommendations for Industry Professionals
For industry professionals, staying informed about the latest coating technologies and trends is essential. Engage with experts, attend industry conferences, and participate in training programs to enhance your knowledge and skills.
When planning a coating project, prioritize thorough research and planning to ensure the best results. Consider all factors, from environmental conditions to application methods, to select the most appropriate coating solution.
Frequently Asked Questions (FAQ)
What are the main benefits of using protective coatings?
Protective coatings offer numerous benefits, including enhanced durability, resistance to environmental damage, and improved safety. They help extend the lifespan of structures, reduce maintenance costs, and protect against corrosion, wear, and fire.
How do I choose the right coating for my project?
To choose the right coating, assess the specific needs of your project, including environmental conditions, material compatibility, and regulatory requirements. Consult with experts to get tailored recommendations based on the latest technologies and industry standards.
Additionally, consider the total cost of ownership, balancing upfront costs with long-term performance and maintenance needs.
Are there environmentally friendly protective coatings available?
Yes, there are many eco-friendly coatings available that minimise environmental impact. These include water-based coatings, low-VOC formulations, and bio-based resins derived from renewable resources. These coatings offer effective protection while adhering to environmental regulations.
Choosing eco-friendly coatings can help industries meet sustainability goals and reduce their carbon footprint, contributing to a healthier planet.