Testing the Heavy-Duty Resilience of Acrylics for Industrial Structures
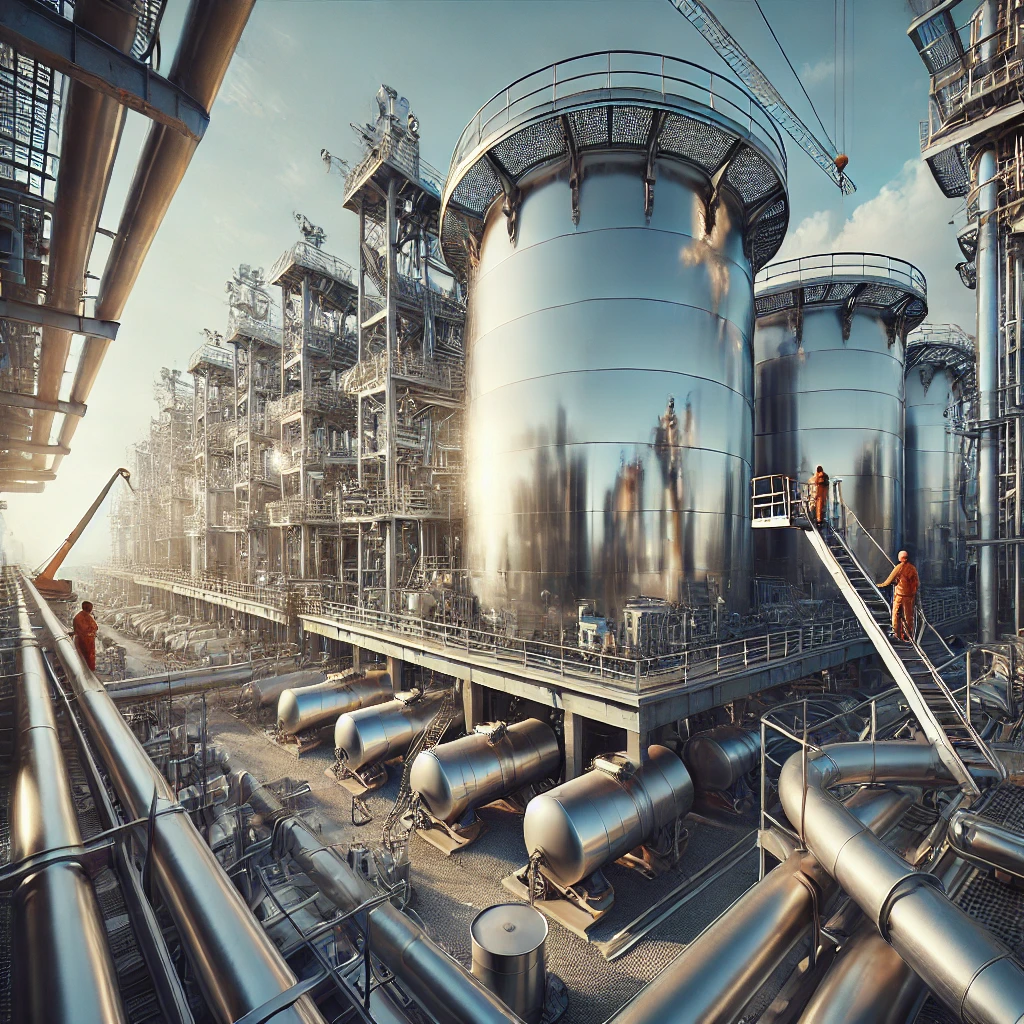
Key Takeaways
- Acrylics are highly valued in industrial applications for their strength, durability, and versatility.
- Impact resistance tests, such as falling weight and pendulum tests, are essential for evaluating acrylic’s resilience.
- Pressure and load-bearing tests help determine how well acrylics can handle heavy-duty industrial use.
- Environmental exposure tests ensure acrylics can withstand harsh conditions like UV radiation, chemicals, and extreme temperatures.
- Understanding the unique properties of acrylics can guide better material choices in construction, automotive, and other industries.
Testing the Heavy-Duty Resilience of Acrylics for Industrial Structures
When it comes to industrial structures, choosing the right material is crucial. Acrylics, known for their strength and versatility, often stand out. But how do we know they’re up to the task? Let’s dive into the importance of testing the heavy-duty resilience of acrylics in industrial settings.
Importance of Acrylics in Industrial Applications
Acrylics are popular in various industries due to their impressive properties. They offer a unique combination of strength, transparency, and resistance to impact and chemicals. These qualities make them suitable for applications ranging from construction to automotive design.
For instance, in the construction industry, acrylics are used for windows, skylights, and even entire facades. Their transparency and strength make them an excellent alternative to glass. In the automotive industry, acrylics are used for headlamp covers and interior components, where durability and aesthetics are essential.
Key Characteristics of Acrylics: Strength and Durability
Acrylics possess several key characteristics that make them ideal for heavy-duty applications. Their high impact resistance means they can withstand significant force without cracking or shattering. This is crucial in environments where materials are subject to sudden impacts or heavy loads.
Additionally, acrylics are highly resistant to various chemicals, including acids and alkalis. This makes them suitable for use in chemical processing plants and laboratories. Their durability also extends to environmental factors, as they can resist UV radiation and extreme temperatures without degrading. For more information, check out the durability of acrylic sheet.
- High impact resistance
- Chemical resistance
- UV radiation resistance
- Temperature resistance
Testing Methods for Heavy-Duty Resilience
To ensure acrylics can handle the demands of industrial applications, we need to subject them to rigorous testing. These tests help us understand how acrylics will perform under various conditions and stresses.
Standard Impact Resistance Tests
Impact resistance tests are designed to measure how well a material can withstand sudden forces. Two common methods are the falling weight test and the pendulum impact test.
In the falling weight test, a weight is dropped from a specified height onto the acrylic sample. The test measures the force required to cause damage. This test simulates real-world impacts, such as debris hitting a window.
The pendulum impact test involves a pendulum striking the acrylic sample. The energy absorbed by the sample is measured, providing insights into its ability to withstand impact forces. This test is particularly useful for evaluating materials used in protective barriers and shields.
Pressure and Load-Bearing Tests
Besides impact resistance, it’s crucial to know how well acrylics can handle sustained pressure and heavy loads. Pressure tests involve applying a constant force to the acrylic sample to see how it deforms or breaks. These tests are essential for applications where the material will bear weight, such as in structural components.
Load-bearing tests, on the other hand, focus on how much weight the acrylic can support before failing. These tests help determine the material’s suitability for applications like flooring or support beams.
Environmental Exposure Tests
Industrial environments often expose materials to harsh conditions. Therefore, it’s essential to test how well acrylics can withstand factors like UV radiation, chemicals, and extreme temperatures.
UV exposure tests simulate prolonged exposure to sunlight, ensuring the material doesn’t degrade or lose its transparency. Chemical resistance tests involve exposing the acrylic to various chemicals to see how it reacts. Temperature tests subject the material to extreme heat and cold to ensure it remains stable. For more information on the durability of acrylic sheet, visit this detailed article.
Environmental Exposure Tests
Industrial environments often expose materials to harsh conditions. Therefore, it’s essential to test how well acrylics can withstand factors like UV radiation, chemicals, and extreme temperatures.
UV exposure tests simulate prolonged exposure to sunlight, ensuring the material doesn’t degrade or lose its transparency. Chemical resistance tests involve exposing the acrylic to various chemicals to see how it reacts. Temperature tests subject the material to extreme heat and cold to ensure it remains stable.
Laboratory vs. Real-World Testing
While laboratory tests provide controlled conditions to measure acrylic’s resilience, real-world testing is equally important. Laboratory tests can isolate specific factors and give precise data, but they can’t always replicate the complexities of real-world environments.
Real-world testing involves using acrylics in actual industrial settings to observe how they perform over time. This type of testing can reveal issues that lab tests might miss, such as long-term wear and tear or unexpected chemical interactions. Combining both approaches ensures a comprehensive understanding of the material’s capabilities.
Impact of Acrylics in Various Industries
The resilience of acrylics makes them valuable in several industries. Let’s explore some key applications.
Aerospace and Automotive Applications
In the aerospace industry, acrylics are used for aircraft windows and canopies. Their high impact resistance and clarity make them ideal for these applications. Additionally, acrylics are lighter than glass, which helps reduce the overall weight of the aircraft, improving fuel efficiency.
In the automotive industry, acrylics are used for headlamp covers, instrument panels, and even body panels. Their durability ensures that these components can withstand the rigors of daily use, including exposure to sunlight, road debris, and varying temperatures. Learn more about high-performance acrylic for industrial surfaces.
Use in Construction and Architecture
Acrylics are widely used in construction and architecture for applications such as windows, skylights, and facades. Their transparency and strength make them an excellent alternative to glass, providing both aesthetic and functional benefits.
For example, acrylic panels are often used in modern building designs to create striking visual effects while ensuring safety and durability. Their resistance to weathering means they can maintain their appearance and structural integrity over time, even in harsh environmental conditions. Learn more about the durability of acrylic sheets.
Applications in Chemical and Manufacturing Industries
In chemical processing plants and laboratories, acrylics are used for protective barriers, tanks, and piping. Their resistance to a wide range of chemicals makes them suitable for handling corrosive substances without degrading.
In manufacturing, acrylics are used for machine guards, display cases, and various other components that require both durability and clarity. Their ability to withstand impact and chemical exposure ensures long-lasting performance in demanding environments.
Benefits and Challenges of Using Acrylics
While acrylics offer many advantages, they also come with some challenges. Understanding these can help in making informed decisions about their use in industrial applications.
Benefits | Challenges |
---|---|
Excellent durability and longevity | Higher initial cost compared to some alternatives |
Superior clarity and light transmission | Less impact-resistant than some materials (e.g., polycarbonate) |
UV resistance and color retention | Can be prone to crazing when exposed to certain chemicals |
Chemical resistance to many substances | Not suitable for very high-impact applications |
Thermal insulation properties | May become more flexible at higher temperatures |
Easy to shape and fabricate | Requires careful handling to avoid scratches |
Weather-resistant | Can be affected by sustained loading (creep) |
Lightweight compared to glass | Not as heat-resistant as some specialized materials |
Good mechanical strength | May require impact-modified grades for tougher applications |
Excellent surface hardness and scratch resistance | Can be attacked by strong acids and some solvents |
Versatility in industrial applications | Potential for static electricity build up |
Recyclability | May require special cleaning procedures |
Good electrical insulation properties | Can be sensitive to stress cracking |
Resistance to corrosion | May yellow slightly over time with UV exposure |
Easy to clean and maintain | Requires proper ventilation during fabrication |
Advantages Over Traditional Plastics and Glass
- Higher impact resistance compared to glass, reducing the risk of shattering.
- Better clarity and transparency than many traditional plastics.
- Resistant to UV radiation and weathering, ensuring longevity.
- Lighter weight than glass, reducing transportation and installation costs.
- Excellent chemical resistance, suitable for harsh industrial environments.
These advantages make acrylics a preferred choice for many applications, offering a balance of strength, durability, and aesthetic appeal.
Potential Drawbacks and Mitigation Strategies
Despite their many benefits, acrylics have some limitations. They can be prone to scratching, which can affect their appearance and performance. However, this can be mitigated by applying scratch-resistant coatings or using protective films.
Acrylics can also be more expensive than some traditional plastics, which may impact project budgets. To address this, consider the long-term benefits of acrylics, such as reduced maintenance costs and longer lifespan, which can offset the initial investment.
Case Studies
To illustrate the resilience and versatility of acrylics, let’s look at some successful industrial projects that have utilized this material. For a deeper understanding of the durability of acrylic sheets, check out this detailed article.
Successful Industrial Projects Utilizing Acrylics
One notable example is the use of acrylic panels in the construction of the Burj Al Arab in Dubai. The building’s iconic sail-shaped design features large acrylic windows that provide stunning views while withstanding the harsh desert environment. The acrylic panels were chosen for their clarity, strength, and resistance to UV radiation, ensuring they remain pristine over time.
Another example is the use of acrylics in the automotive industry by Tesla. The company uses acrylic for the panoramic roofs of their Model S and Model X vehicles. The material’s high impact resistance and transparency enhance the driving experience while ensuring passenger safety. Learn more about the durability of acrylic sheet.
Lessons Learned and Best Practices
These case studies highlight the importance of selecting the right material for specific applications. When using acrylics, consider factors such as environmental exposure, impact resistance, and long-term durability. Proper testing and real-world evaluations can help ensure the material meets the demands of the application, including the use of industrial acrylic primers.
Additionally, incorporating protective measures, such as scratch-resistant coatings and UV inhibitors, can enhance the performance and longevity of acrylics in industrial settings.
Future Prospects of Acrylics in Industrial Structures
The future of acrylics in industrial structures looks promising, driven by continuous innovations and technological advancements. As industries seek materials that offer a blend of strength, durability, and aesthetic appeal, acrylics are likely to play an increasingly significant role.
Innovations and Technological Advancements
Recent innovations in the production and processing of acrylics have enhanced their properties and expanded their applications. For example, advances in polymer chemistry have led to the development of acrylics with improved impact resistance and chemical stability. These new formulations are better suited to withstand the demanding conditions of industrial environments.
Technological advancements in manufacturing processes, such as injection molding and extrusion, have also improved the quality and consistency of acrylic products. These processes allow for the production of complex shapes and large panels with precise dimensions, making acrylics more versatile and adaptable to various industrial needs. Enhance outdoor durability with weather-resistant paints to further increase the resilience of acrylic structures.
Moreover, the incorporation of advanced coatings and additives has further enhanced the performance of acrylics. Scratch-resistant coatings, UV inhibitors, and anti-glare treatments are now commonly used to protect acrylic surfaces and extend their lifespan. These enhancements make acrylics more resilient and suitable for a broader range of applications.
For example, the development of anti-static coatings for acrylics has been a game-changer in the electronics industry. These coatings prevent dust and particles from accumulating on acrylic surfaces, ensuring clear visibility and reducing maintenance requirements.
Potential for Expanded Use Beyond Current Applications
The versatility and resilience of acrylics open up exciting possibilities for their use beyond current applications. One area with significant potential is the renewable energy sector. Acrylics can be used in the construction of solar panels and wind turbine blades, where their transparency, strength, and weather resistance are valuable assets.
Another promising area is the medical field. Acrylics are already used for medical devices, lenses, and protective barriers. With ongoing research and development, acrylics could be further optimized for use in advanced medical applications, such as implantable devices and diagnostic equipment.
Frequently Asked Questions (FAQ)
To address common queries about the resilience and applications of acrylics in industrial structures, here are some frequently asked questions. For more detailed information, you can also explore high-performance acrylic for industrial surfaces.
What Makes Acrylics Stronger Than Other Plastics?
Acrylics are stronger than many other plastics due to their unique molecular structure. The polymer chains in acrylics are tightly packed, providing high tensile strength and resistance to impact. Additionally, acrylics have a higher molecular weight compared to some traditional plastics, contributing to their superior performance.
The chemical stability of acrylics also plays a role in their strength. They are less prone to degradation when exposed to UV radiation, chemicals, and extreme temperatures, ensuring long-lasting durability in various environments.
How Are Acrylics Tested for Heavy-Duty Applications?
Acrylics undergo several rigorous tests to ensure their suitability for heavy-duty applications. Impact resistance tests, such as the falling weight test and pendulum impact test, measure the material’s ability to withstand sudden forces without cracking or breaking. Learn more about high-performance acrylic for industrial surfaces.
Pressure and load-bearing tests assess how well acrylics can handle sustained pressure and heavy loads. These tests involve applying a constant force or weight to the material to observe its deformation or failure point. Learn more about choosing acrylics for transportation durability.
Environmental exposure tests simulate harsh conditions, such as prolonged UV exposure, chemical contact, and extreme temperatures. These tests help determine the material’s resilience and stability under real-world conditions.
What Are the Common Uses of Acrylics in Industry?
- Construction: Windows, skylights, facades
- Automotive: Headlamp covers, instrument panels
- Aerospace: Aircraft windows, canopies
- Chemical processing: Protective barriers, tanks, piping
- Manufacturing: Machine guards, display cases
Acrylics are valued in these applications for their transparency, strength, and resistance to impact and chemicals. Their versatility and durability make them suitable for a wide range of industrial uses. For more information, check out choosing acrylics for transportation durability.
In conclusion, the resilience of acrylics makes them an excellent choice for various industrial applications. By understanding their properties and testing methods, we can make informed decisions about their use in demanding environments. As innovations and technological advancements continue to enhance their performance, the future of acrylics in industrial structures looks bright.
Whether you’re in construction, automotive, aerospace, or chemical processing, acrylics offer a reliable and versatile material option. Embrace the potential of acrylics to improve the durability and efficiency of your industrial projects.